Our Technology
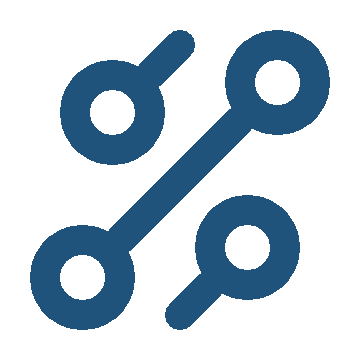
What Makes Nautilus Systems Special?
>Capture >Peel >PlaceTM – that’s what makes us special.
>Capture >Peel >Place is a phrase we coined to describe our technology and methodology for adhesive component placement and to differentiate ourselves from ‘old world’ labeling systems. The pictures below show the > Capture >Peel >Place method in action. Note that the label or die-cut adhesive component is always controlled, either by being attached to the liner or by being captured by our vacuum chuck:
Now compare that to traditional labeling systems using the process we refer to as Flutter, Float, Levitate, and HopeTM. You will see that there is a vast difference between the two technologies. The traditional technology uses a combination of puffing air and vacuum to float/levitate the label from the liner to the vacuum head as the liner advances. It is a very uncontrolled process.
It’s easy to understand that > Capture >Peel >Place is a superior method. Unlike traditional labeling systems our innovative design provides a system that can remove virtually any adhesive component from a roll and place it onto a substrate with extreme reliability and high precision. > Capture >Peel >Place allows us to: >Capture the adhesive component while it is still attached to the liner (roll); >Peel the liner away from the adhesive side of the component; and >Place the component onto the desired target. This method maintains control of the component at all times. Components can include all types of roll-fed die-cut materials including labels, insulating tapes and films, conductive tapes and foils, gasket materials, medical materials, hang tabs, multi-layer materials, and more. Likewise, our systems are not affected by the shape of the material. We can > Capture >Peel >Place components that are rectangular, round, frame-shaped, odd-shaped, and even capture multiple detached arrays of components simultaneously. Any material and any shape of component can be automatically applied with this technology. That’s why we’ve become a standard solution for industries as diverse as Packaging, Automotive, Medical Device, Energy, Semiconductor, Mobile Device, Electronics, Consumer Goods, and more.